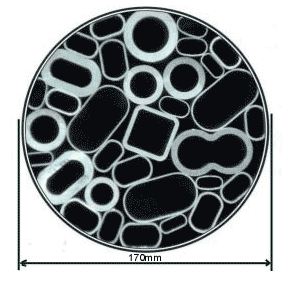
Precision Tube Production - Services
At Precision Tube Production we are committed to providing a first class service, so contact our experienced sales team on 01844 463103 or email sales@drawntube.com to discuss your requirements.
Whilst the majority of production relates to aluminium round tubes, we also have extensive fabrication facilities for tube bending, aluminium welding and assembly.
Tube Welding:
PTP has many years’ experience in welding aluminium components. Our welding capability is fully coded and we weld aluminium Tubes, Extrusions, aluminium components to customers’ requirements.
Welding has many advantages compared to other joining techniques, for example:
- It is possible to weld materials of differing thicknesses – between 2mm and up to several centimetres thick.
- Welding is one of the safest and easiest methods of creating airtight and watertight joints.
- Overall welding can be a cost effective method of joining materials.
The most common fusion welding methods are tungsten inert gas welding (TIG) and metal inert gas welding (MIG). Both these processes provide good results. The thickness of the parts to be welded determines the amount of filler required – fillers are standardised and are available as coiled wire or rods. Coiled wire is generally available in 1.2mm and 1.6mm diameters and is applicable only to MIG welding.
Rods are generally available in diameters ranging from 1.6mm to 6.4mm. Filler rod diameters cover a range of metal thicknesses from 0.7mm to 10.0mm.
During welding it is vital that the filler used is clean and dry and that the surface is cleaned prior to use to remove any contamination.
MIG Welding
MIG Welding has been developed from TIG welding to allow a speeding up of the welding process. The difference between MIG and TIG welding is that MIG welding utilises a filler welding wire as the electrode to create the arc instead of a tungsten tip. This method can be used to create all types of joints and all welding positions.
MIG welding is generally used for material thicknesses ranging from 3mm upwards.
The main advantage of this welding method is that it has a high welding speed and good penetration. The width of the heat affected zone is less than with any other welding process due to the speed of the process. Therefore welding deformation is less with MIG than it is with TIG welding.
However MIG welding is less successful when short weld runs are made or where the joints are not easily accessible. The inert gas used for optimum performance when MIG welding is Argon.
TIG Welding
TIG Welding does not require flux because it also uses an inert gas shield (Argon) to protect the weld pool from oxidisation. This makes the use of this welding method particularly suitable for aluminium welding.
It is used mainly for materials ranging from 2mm to 10mm thick and also for welding shorter joints. TIG welding can be carried out on all suitable aluminium alloys.
Site Sponsored by AircraftmaterialsUK.com Ltd